Make/Use: Flat to Form
This workshop was about understanding the construction of a Make/Use garment from two dimensional flat pattern, to finished three dimensional form. Utilising the screen printed Make/Use T shirt flat, participants were guided through the creation of their own individualised T shirt from the 48 different possible outcomes the pattern allows. A group of participants with varied backgrounds and levels of sewing experience engaged in this novel process – with amazing results.
The System
The Make/Use system is unlike any traditional garment construction process, and as such, requires a different cognitive understanding of the relationship between flat fabric/pattern and garment form. This seemingly complex shift in thinking is in fact very simple. The whole system hinges on two basic concepts, the first being the creation of volume through the joining of two edges of a piece of fabric to form a tube – a space for the body to pass through. The basic Make/Use T shirt pattern can be understood as two conjoined tubes: a vertical one for the torso, and a horizontal one for the sleeves and shoulders, with a neck hole that allows the garment to pass over the head. The second concept deals with the manipulation of those tubular volumes, which is essentially achieved through the slicing of the tube at an angle, followed by a rotation of one end through 180 degrees to form a ‘bent’ tube. In fabric, this bend may translate to the shaping of a sleeve, or the alteration of the drape around the lower body, creating more volume at the back while raising the front hem.
Participants in the Flat to Form workshop explored these concepts through playing with paper scale models of the T shirt pattern. This unintimidating method, which has similarities with the Japanese art of origami, is not only a fun and easy way of providing a first engagement with the system, but also reflects one of the techniques that designer Holly McQuillan uses to quickly test and iterate zero waste design ideas.
The Construction Process
Having gained confidence and understanding of the core concepts of the Make/Use system, workshop participants explored opportunities for customization of the T shirt pattern, using both the paper models and half-scale calico versions. In this workshop, the paper and fabric ‘flats’ were pre-printed with the print pattern developed by Greta Menzies in collaboration with the Make/Use team. This print pattern is both aesthetic and informative – it encodes navigational cues into the print that operate as way-showing devices for the user to aid in construction and decision-making. Rather than presenting a prescribed set of instructions, the way-showing system was conceived as an intuitive ‘landscape’ of mark-making that the user could negotiate in their own way, while retaining a sense of security and orientation provided by route markers at key points of connection or intersection.
The workshop beautifully illustrated the benefits of this design strategy. Not only were participants empowered to engage with the embedded opportunities for modification, some even quickly moved on to exploring their own ‘hacks’, uncovering new possibilities. While some of these moves proved more successful than others, they nevertheless demonstrated the ability to test and adapt the pattern to suit the tastes and desires of individual maker/users.
The Finishing Detail
In the second half of the workshop, participants moved on to a full size pre-printed T shirt ‘flat’. Prior to cutting and sewing, the group was introduced to different possibilities for pre-finishing the edges to be cut, which allows for future modification and the re-setting of the fabric back to flat cloth. Beyond the more obvious methods of hand or machine sewing, and the less accessible high-tech option of digital embroidery, a much more low-fi, quick and engaging method was demonstrated – hand painting directly onto the fabric with acrylic house paint. In encasing the fibres, the paint provides a flexible and user-friendly edge finishing technique, and can also offer opportunities for personalized decorative mark-making and creation of visual interest through colour selection.
Once pre-finished, the fabric flat is cut and assembled according to the design decisions made by the maker/user. Again a variety of seam joining options is available, including machine and hand stitching. The Make/Use display collection also includes a coat that uses needle-felting as a joining technique.
A key feature of the Make/Use garments is their ability to be re-set and re-made. In some instances a special hand-stitching technique, called an insertion stitch, is used to facilitate this re-joining. The insertion stitch is relatively simple to implement and is both functional and effective to look at, drawing the eye to this detail. It forms a kind of conspicuous mending, borrowing from the Japanese concepts of kintsugi and kintsukuroi: the art of the beautiful repair.
_
Make/Use would like to thank the participants in this first workshop. You are pioneers in what we hope will become a growing community of maker/users. We trust you enjoy your garments as much as we enjoyed helping you to create them!
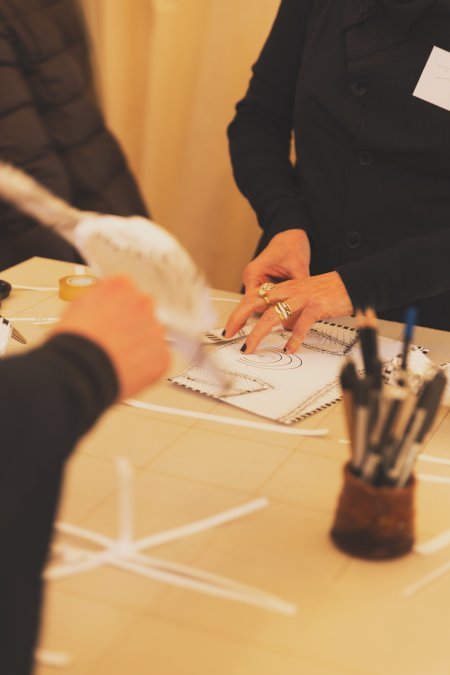